Norwich and Norfolk University Hospitals
We have central water purification systems supplying our busy endoscope reprocessing and sterile services departments. Each consists of softener, carbon filter, twin RO and a ring main with heat sanitisation. Lubron Water Technologies’ is one of best contractors that I deal with: the equipment is high quality and really well engineered. They carry out regular maintenance to keep the systems running efficiently and design alterations to clients’ specifications.”
Alan Parkins
Lead Decontamination Engineer, Serco Services, Norfolk & Norwich University Hospital
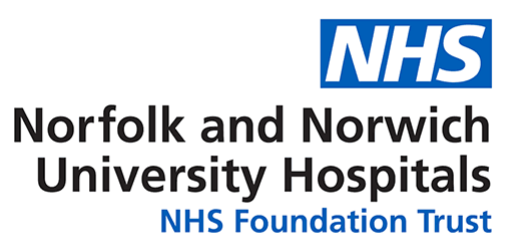
Wight Salads
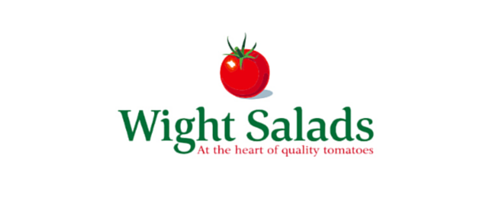
Annual water consumption for the Island’s five sites is about 120,000m3, roughly 70% of which comes from collected rain water run-off from the glasshouses,” says Darren Oatley, Plant & Facilities Manager at Wight Salads, part of the APS group, “The balance is from boreholes. The only mains water we use is for the drinking water taps and kitchens.” The borehole water has a significant concentration of dissolved iron. Using this water for spray irrigation would result in black deposits on the leaves and fruit, so it is vital that this is removed. “Each of our vineries is provided with a Lubron Water Technologies iron removal filtration system, which ensures that only iron free water is supplied to the plants. These are serviced annually when the plants are not too big that they need constant watering, and have never gone wrong. The filters are backwashed to remove the accumulated iron, and this waste water is treated in our own reed beds before discharge.”
Darren Oatley
Plant & Facilities Manager at Wight Salads
University Hospital Southampton
We talked with Lubron Water when we first began specifying the Reverse Osmosis (RO) plant for the Endoscopy Unit and wound up working right the way through to installation and delivery. Installation was quite tricky because there was limited space in the plant room so it was very much a bespoke engineered solution.” Commenting on the new water treatment plants, Jean Hedges said “It’s improved the water quality no end. Because the units are twin pass, the high silica is removed to safe levels and we have had no microbiological issues. And both projects came in on budget.”
Jean Hedges
Southampton General’s Decontamination Manager
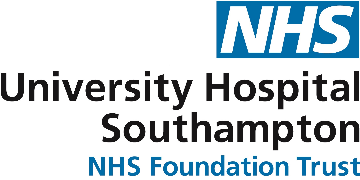